Warehouses and distribution centers grow together with the e-commerce and retail industry. With that growth comes a new level of difficulties and complexities that need to be addressed. The need for faster order fulfillment, more inventory, more SKUs (Stock Keeping Units), and better-utilized space.
Adapted slotting in a warehouse is a solution that can address these issues without the need to expand your workforce or warehouse, but just the SKU location within the warehouse.
Introduction To Warehouse Slotting
Slotting in a warehouse is a form of inventory management which means organizing the inventory for optimal space efficiency, order picking, and refilling. Warehouse slotting involves analyzing what are the optimal ways of storing your inventory by item size, weight, SKU velocity (or sales rotation) and order frequency, and many other factors.
While warehouse slotting is spoken of as one phenomenon, it can be divided into 2 processes. These terms aren’t too widely used, but it is still beneficial to be familiar with them. In this article we will talk about both – micro slotting and macro slotting – as one common unit.
- Micro-slotting accounts for the arrangement of inventory within a picking zone – the optimal way of item arrangement on a shelf or an aisle. SKUs with higher demand should be more accessible, whilst heavier, or more unstable items should be placed lower, to increase the safety of the employee and inventory.
- Macro slotting is broader. It accounts for the arrangement of the picking zones and the warehouse layout. While micro slotting principles can be similar to all warehouses, macro slotting differs for small to large warehouses and distribution center layouts.
One can also take 3 different approaches for optimizing slotting within a warehouse based on specific business needs.
- From-scratch slotting is applied when the majority or the entire warehouse needs to be re-slotted, rearranging the SKU locations from scratch. This would be the case either for new warehouses or distribution centers which would use an algorithm with their order history or data reference to come to the optimal slotting layout.
This method can be used as an A/B testing for multiple warehouses or distribution centers to see which SKU arrangement plan suits best and has the biggest impact on total pick distance. - Incremental slotting takes into account the current SKU locations within the warehouse and the cost of re-slotting current SKUs. This method can be used when order dynamics have changed drastically which would make SKU re-slotting recommended.
- Dynamic slotting indicates the best currently available slot for a new inbound order. Dynamic slotting doesn’t use dedicated, fixed SKU locations, but flexibly chooses the best available slot.
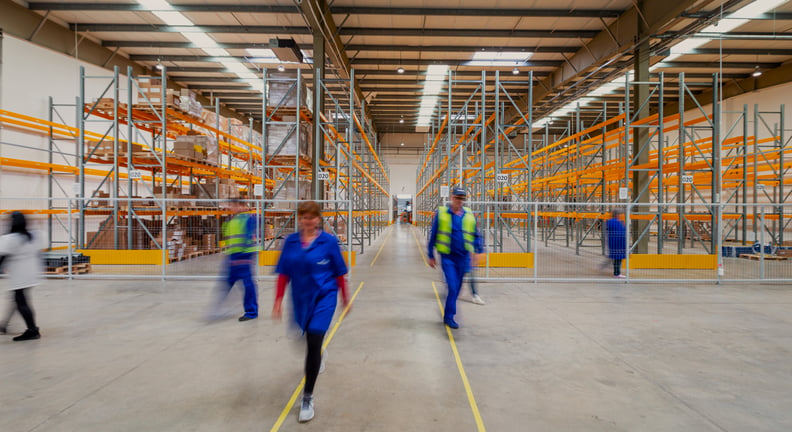
Benefits of Slotting
Slotting a warehouse can be a difficult and costly task, but choosing the right methods and solutions, and optimizing the inventory arrangement and placement can create a significant increase in operational efficiencies and improved handling, resulting in saved resources, time, and money, and many other benefits.
Lower pick distance and faster order fulfillment
By optimizing warehouse slotting, pick distances can decrease from 10 % to 30 %, decreasing the travel time of the pickers and increasing order fulfillment time. Another benefit is decreased time of inventory sitting in a warehouse, allowing more items to flow through the space. Picking is, on average, 50% of the total warehousing cost. Slotting has a direct impact.
Safety of inventory
Since slotting takes into account the constraints of the items, such as weight, size, and special requirements (hazardous, easily flammable, temperature sensitive, high-security) - inventory can be arranged taking into account these variables. For example, heavier items placed on the bottom of the shelf and lighter ones on the top would ensure the stability of the shelf.
Fully utilized space
By slotting your warehouse in the most suitable way for your business, you can maximize the utilized storage capacity. Efficient slotting can lead to storing more items in one area, leading to more space for new inventory. Especially when taking into account the slot and pallet heights.
Optimized Picking and Packing
Slotting can increase the efficiency of picking and packing as well. Some of the ways include arranging items closer which has higher item correlation (or product affinity), having multiple picking stations for one SKU, or having forklift necessary picking zones separated from smaller item picking zones to decrease the congestion in certain aisles which can cause delays in order fulfillment.
Complexities of Slotting
It is not deniable that warehouse slotting can significantly increase the efficiency of warehouse workflows, but many complexities still exist when adapting the optimal warehouse slotting principles to your business. That’s why it’s crucial to identify them and take them into account.
Size and weight
Heavier items need to be placed lower on the shelves to make sure they aren’t too top-heavy, and the center of gravity isn’t too high up in order to increase the stability of the picking stations and worker safety. Another crucial factor is making sure that the size of the inventory is in the optimal slot rather than taking too much space in a larger-than-necessary spot or having the need to split the pallet for it to fit.
Stacking priorities
When items are stacked on top of each other in the warehouse, the sequence in which they are stacked is important, since the picker cannot get to the items at the bottom without removing the top ones. The size and weight complexity also come into play here, since the rearrangement of items to get to the bottom item can bear too much stress on the picker.
SKU velocity (Item demand)
Items that are most frequently picked from the picking stations or have the highest SKU velocity should be placed closer to the packing station than items that have a lower SKU velocity and move slower out of the warehouse. Order history can help you conclude which items have the highest SKU velocity and deserve a slot closer to the packing stations and which items can be deprioritized and moved further away.
However, this can lead to high traffic in certain aisles decreasing order fulfillment time. Additionally, new questions arise – what would be the optimal item shelving approach for high SKU velocity items? How does seasonality affect the velocity of SKUs? How should I re-slot the warehouse depending on seasonality?
Product affinity
Efficient slotting also considers product affinity - what customers purchase together in one shopping trip. Keyboards with mice and darts with dartboards shouldn’t be placed too far apart from one another. This factor also affects the slotting principles of your warehouse.
In some instances, having multiple slots or shelves dedicated to one product can be beneficial to warehouse layout due to the diverse product affinity.
How To Optimize Slotting
Analysis of order history can be done by applying the ABC analysis, which is a way of determining the optimal slot for each SKU, depending on SKU velocity.
The principle of ABC analysis includes listing all SKUs which have been ordered over a certain period of time (the longer the time period, the more accurate the data). Then the SKUs are divided into 3 categories – A, B, and C.
Then depending on your warehouse size and SKU diversity, each category has an allocated percentage. In this example the top 40% of the SKUs (the most frequently ordered items) fit in the A category, the following 25 % of SKUs will fit into the B category, and the next 25 % will fit into the C category. It can be concluded that depending on the category it can be arranged based on their demand frequency. The A category items will be arranged closest to the picking area while the remaining 10% of the SKUs can be put farthest away from the ABC category’s SKUs.
Another way to quickly gain some insights on ways to improve your warehouse slotting is creating heatmaps of:
- Rotation class of items in every warehouse slot
- Picker's most common routes in a warehouse
Which can inform you of simple and quick re-slotting options.
Advanced approach
If you are looking to improve your slotting by taking into account SKU velocity, weight, dimensions, product affinity, and stacking priorities, then you have to resort to AI-powered and data-driven slotting software.
A critical step in getting the most out of AI-powered software is implementing an automated dimensioning system. An automated dimensioning system is made to provide quick and accurate dimensions of each SKU coming into a warehouse.
A dimensioning system combined with slotting allows you to know how much current space is occupied and how much space is available, allowing you to have up-to-date data for just-in-time inventory management.
With a dimensioning system, SKU dimensions can be automatically imported into a warehouse management system which significantly simplifies the process of determining how and where to arrange inventory for optimized pick density and decreased order fulfillment time, by taking into account the size of the available warehouse slots.
Conclusions
When planning the first steps for a warehouse slotting strategy a good starting point is applying the ABC analysis - listing all SKUs which have been ordered over a certain period and then allocating each SKU’s category to a certain location in a warehouse depending on its priority.
For a new distribution center or warehouse, a more suitable way would be the from-scratch slotting method - rearranging the SKU locations from scratch – using order history or reference data to come to the optimal slotting layout.
For improvements in existing slotting strategies, an incremental slotting approach would be more suitable since it considers the cost of re-slotting of current SKUs.
For a more sophisticated and advanced approach implementing an automated dimensioning system would take warehouse slotting to the next level – combining dimensioning and slotting would allow you to know how much current space is occupied and how much space is available.
While it takes time and analysis to determine the optimal layout and SKU arrangement throughout a warehouse, warehouse slotting is something that can certainly be a solution to more efficient warehouse operations, saved costs, faster order fulfillment, and even more satisfied customers.